Callaway XR 16 driver: Why Boeing?
Boeing senior techie Jeffrey Crouch explains why the aircraft specialists joined forces with Callaway
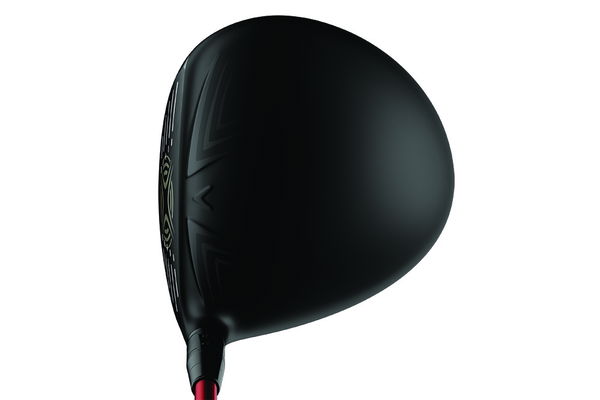
NEW: Callaway XR 16 driver review
What attracted Boeing to work on the XR 16 driver with Callaway?
Boeing is committed to the professional development and growth of its technical workforce while delivering business results.
One way this is achieved is providing people with special ‘experiential’ opportunities to learn from others inside and outside of Boeing. We believe cross-industry collaboration is beneficial to all involved.
Our engineers have great depth of knowledge and expertise that can be leveraged in numerous other fields.
First Look: Callaway XR 16 driver video review
This project, in particular, was viewed as a special career rotation assignment during which the Boeing participants could be exposed to a short-flow product development and innovation cycle, while also providing their technical expertise to supplement the talent of the Callaway team.
I thought it would be cool to learn about the physics of golf and to have a chance to apply my knowledge and experience to help improve a Callaway driver.
What are the key principles of aircraft design that transfer into golf club technology?
Reducing drag and controlling the flow to achieve the most efficient aerodynamic performance is a critical part of airplane design. Those same principles applied to this project with Callaway.
The speed and size of the golf club are more like a wind-tunnel model than a full-scale airplane, so wind tunnel test techniques are also helpful.
What are the aerodynamic challenges involved in designing drivers and how do these differ vs your day job?
This was a new challenge for Boeing; also a unique challenge for the engineers involved.
An aircraft moves through space with relatively slow changes in orientation; the driver is a different challenge because it moves through space with rapid changes in orientation. As a result, any aerodynamic improvements must be effective over a wide range of flow conditions.
One of the things I work on at Boeing is laminar flow control, which seeks to delay turbulence and increase the amount of laminar flow on aerodynamic surfaces. This reduces airplane drag and leads to reduced fuel consumption and lower emissions.
For driver design, because of its bluff shape we wanted to trigger turbulence in order to reduce drag. In this case, the goal was increased head speed, which translates to more distance on the golf course.
What specific inputs Boeing has had in the new XR 16 driver?
Boeing helped with flow modifiers or trip steps; specifically the location and sizing of the trip step to help reduce drag from the top of the swing through impact with the golf ball.
What did you learn from Callaway?
We learned about short-flow product development cycles and innovation.
For example, a typical development cycle for a commercial jet is five to seven years. Callaway on the other hand, develops products on a much shorter timeline.
We also got to see how they used prototyping to evaluate different design elements and to guide their design decisions. Of course, we also learned a lot about the physics of golf.
Was there anything that surprised you?
I would not say that I was surprised, but I did learn many new things about golf physics and it is a very rich problem.
How would you compare the Callaway R&D process to what you do in the aerospace industry?
Both companies share the same goal of producing the most technologically advanced products in their respective industries, and both companies need to design within a highly regulated design space (USGA or the FAA).
The biggest difference is the time spent on the R&D process. Again, typical development cycle for a commercial jet is five to seven years. Golf companies like Callaway, however, develop products on a much shorter timeline.